La ciudad de Charleston, Carolina del Sur, recibió a 17 profesionales costarricenses en la tercera edición del Lean Camp. Esta actividad de “benchmarking” nos permite visitar las instalaciones de los mejores practicantes de Lean y Six Sigma en el mundo. El College of Charleston, una de las universidades más prestigiosas y con más historia en los Estados Unidos fue nuestra institución anfitriona. Los doctores Gioconda Quesada y Marvin González del departamento de Supply Chain and Information Technology, ambos costarricenses radicados en Charleston, fueron los organizadores principales. Además tuvieron el apoyo del “chair” del departamento el Dr. Joshua Davis.
Por el lado de Costa Rica participaron los líderes de lean, six sigma, mejora continua de Hollogic, Boston Scientific, Vitec, AGM, Panduit, BAC-Credomatic y un buen contingente de PXS. Es importante mencionar que todas estas empresas son excelentes referentes de las metodologías de operaciones, calidad y mejora continua, sin embargo el espíritu de la mejora los lleva a conocer qué están haciendo otras compañías, sobre todo de mucha mayor escala y tamaño.
Este es un resumen de la excelente semana de trabajo y visitas.Los Lean Campers en el College of Charleston con nuestros anfitriones
LUNES 13 DE ABRIL. COLLEGE OF CHARLESTON Y BOEING
En la mañana iniciamos con una breve caminata por Charleston y conocimos como la universidad se mezcla con la ciudad, una de las 10 más hermosas de los Estados Unidos. Luego de la caminata los Lean Campers tuvieron la oportunidad de presentar sus empresas a un grupo de estudiantes. Debido a limitaciones de tiempo solamente tres empresas pudieron presentar, pero quedó claro que Vitec, Boston Scientific y Panduit son practicantes de avanzada de Lean Manufacturing.
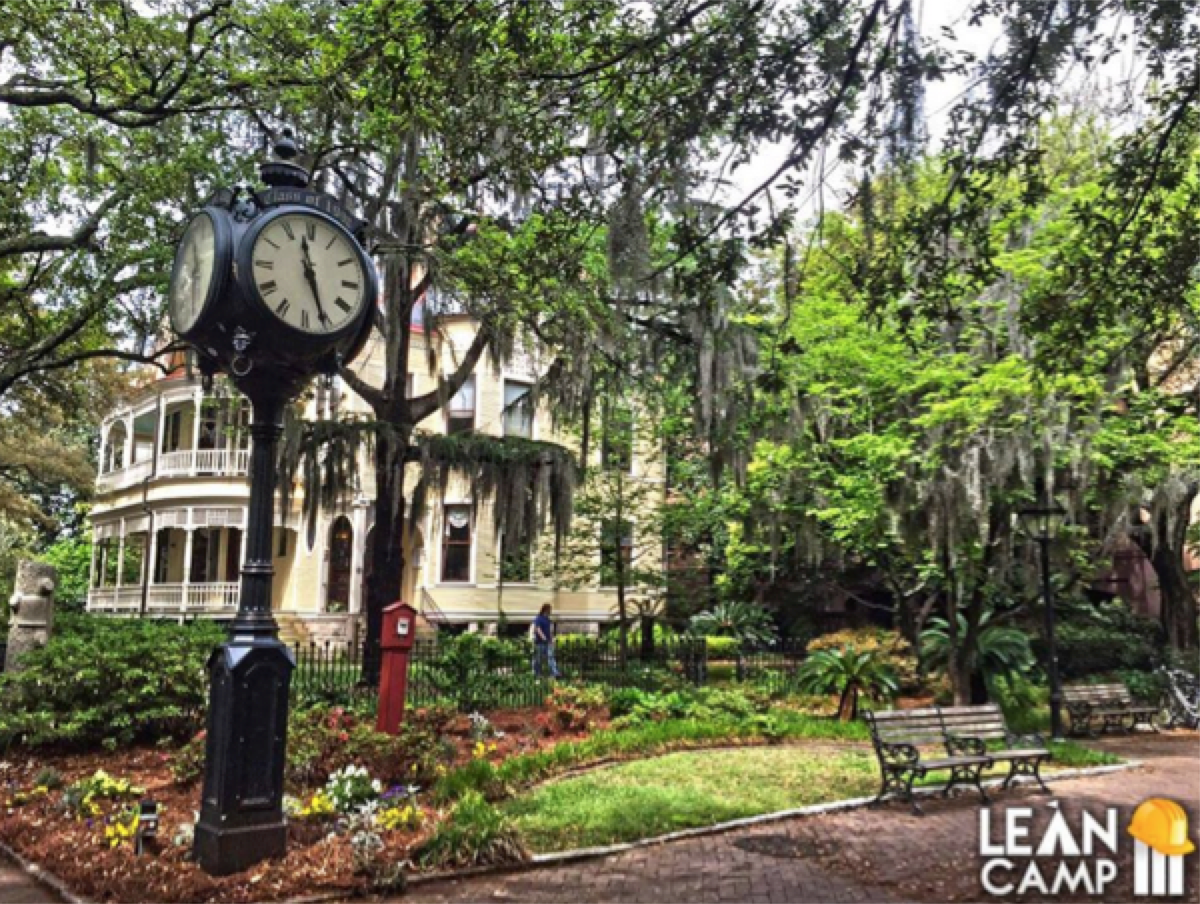
Típica esquina de la ciudad de Charleston
Para la tarde teníamos la primera gran visita a la planta de Boeing en Carolina del Sur. No es fácil explicar la escala de una de las tres plantas de producción donde 7 aviones Dream Liner 787 pasan por alguna de las 7 estaciones de ensamble. Estamos hablando de 6 pisos de alto, en un cuadrado de 400 metros por 400 metros, y este es uno de tres edificios, sin contar el proceso de pintura que por ahora se ejecuta en Texas. Las tres primeras estaciones permiten el ensamble de grandes partes y las alas para dar forma al avión, ya en la tercera estación el 787 descansa sobre su propio tren de aterrizaje. Aparte de los grandes ensambles la mayoría del trabajo se da dentro de los aviones. La primera gran lección del Lean Camp III fue conocer que en la planta nunca hay absolutamente nada que no sean herramientas o partes, cada vez que se termina un trabajo de ensamble los operarios deben hacer una auditoría para comprobar que tienen todas sus herramientas y que usaron todas las partes de los kits correspondientes. La operación de manufactura es totalmente visual y se practica la mejora continua desde administración de sugerencias hasta sistema de Green Belts y Black Belts.
MARTES 14. PUERTO DE CHARLESTON Y CHARLA CON LEANCOR
Otra operación de escala impresionante. El Puerto de Charleston es uno de los más grande y eficientes de los Estados Unidos. El sindicato de empleados es el primero en cumplir con la misión de “Promover al desarrollo económico del estado de Carolina del Sur”. Constantemente miden su productividad, por ejemplo se manejan con un estándar de mover 43 contenedores por hora por barco, los choferes que llegan a dejar un contenedor salen en 22 minutos. Por este puerto BMW exporta 260,000 autos por año. Los equipos de trabajo, llamados “gangs”, tienen sesiones de mejora continua y sus ideas son implementadas cuando son aceptadas.
Para la sesión de la tarde nos trasladamos al moderno campus norte del College of Charleston. Ahí nos esperaba Ana Bailey, experta en lean de la empresa LeanCor que tiene una historia muy interesante. Inicialmente LeanCor fue una empresa de logística, con el tiempo fueron desarrollando un sistema de cadena de abastecimiento que incorporó Lean como una forma de agilizar operaciones de forma integral, incorporando proveedores, operaciones y clientes. El concepto central es Costo Total de Abastecimiento. Ana dominó totalmente la sesión con conocimiento y calidad de exposición, y nos mostró lo que esta empresa llama el formato “A33” que es una extensión muy visual de todo el despliegue que una empresa requiere para agilizar sus operaciones, iniciando con el compromiso y trabajo de alta gerencia. Un importante consejo de Ana, no obligue a sus empleados a usar las herramientas si no saben para qué fin.
Ana Bailey de LeanCor y en el fondo el Formato A33
MIERCOLES 15. EZgo
Cambio de estado. El miércoles nos fuimos hasta Augusta, Georgia, a más de 300 kilómetros de nuestro centro de operaciones. El viaje valió la pena. Llegamos a EZgo, empresa que se dedica a la manufactura de carritos eléctricos, principalmente para campos de golf. Nos recibió Meredith Brazeal, gerente de comunicaciones y relaciones con la comunidad, y luego de una breve introducción pasó la batuta a Dwayne Brabham, gerente de mejoramiento continuo. La empresa es ganadora del Premio Shingo, con la particularidad de que aplicaron, y ganaron, como empresa completa, no sólo como manufactura. Todas las posiciones gerenciales requieren al menos certificación Green Belt y si es posible Black Belt. Se consideran una empresa Lean desde sus bases. Una característica interesante es que los Black Belts permanecen en sus posiciones y dedican entre un 30% y un 40% a proyectos de mejora. Aplican DMAIC en sus áreas de trabajo. Los resultados de los proyectos de mejora son parte de la evaluación del desempeño y determinan el monto del bono anual.
JUEVES 16. MESA REDONDA CON ASTEN JOHNSON
Regresamos a la universidad para una mesa redonda con ejecutivos de AstenJohnson. Esta empresa produce papel, y fibras de alta tecnología. Por parte de la empresa participó un panel de lujo con Mike Benton, Gerente de Educación, Steve Eberhart Líder Corporativo de Mejoramiento Continuo en Lean y Seguridad, Charlie Abraham, Vicepresidente de Desarrollo Estratégico de Negocios y Andrew Blevins, Líder de Cadena de Abastecimiento. Dos grandes empresas familiares se fusionaron creado serios problemas de comprensión entre ambas culturas. En el año 2002 la Junta Directiva decide que Lean será en adelante el lenguaje común de la corporación. El uso de Lean y Six Sigma se da desde diseño y no sólo en manufactura. En el transcurso de los años el sistema ha ido madurando para consolidar la cultura de desempeño de la compañía. La empresa acostumbra hacer muchas adquisiciones y las técnicas lean se han convertido en la herramienta que les permite crear un rápido lenguaje común fácil de asimilar.
VIERNES. LA CEREZA EN EL PASTEL. BMW
El último día otra vez recorrimos un largo camino. Más de tres horas de manejar nos llevaron a BMW, Carolina del Sur, donde se fabrican todos los X3, X4, X5 y X6 de la marca alemana. Nos atendió Eric Hayler, Master Black Belt de la planta, y miembro de la Junta Directiva de ASQ. La visita fue muy detallada y amplia. Visitamos toda la fábrica y vimos de primera mano una operación completamente visual, donde todos saben qué deben hacer y en todo momento cómo lo están haciendo. El Tiempo Takt de la planta es 93 segundos, lo que quiere decir que cada 93 segundos sale un carro terminado. Cada auto fabricado ya está vendido y es totalmente personalizado. Eric nos contaba que puede pasar un año sin repetir un carro exactamente igual. En una ocasión el rey de un país árabe pidió un carro para su hija con el requerimiento de que fuera de un cierto tono de naranja. Fue necesario desarrollar completamente el color y tener a tiempo el pedido de la princesa. Por supuesto ahora es posible pedir un BMW anaranjado. La planta espera producir 400,000 autos este año. Si existe un problema en la operación, hay 93 segundos para arreglarlo, o sino detener la operación. Interesantemente los problemas se avisan mediante un tema musical popular, por ejemplo Help de los Beatles. Nos tocó escuchar Beat It de Michael Jackson, apuntando a que existía un problema en el ensamble del interior de los modelos que se estaban haciendo en ese momento. Vimos gran cantidad de supermercados lean, tableros, pizarras y monitores gemba, luces andon, operación 6S, infinidad de poka yokes, y todo lo que significa un paraíso de manufactura esbelta. Los conceptos japoneses son ahora tan estándar que hasta los alemanes los practican.
LAS GRANDES LECCIONES DE LEAN CAMP
- Las empresas de clase mundial usan Lean Enterprise como la manera de formalizar sus operaciones.
- Lean Enterprise se ha convertido en un lenguaje estándar para el manejo de operaciones, no es una opción ni algo para ir probando, es LA forma de operar.
- La mejora continua tiene varias facetas, desde los sistemas de administración de ideas hasta los proyectos DMAIC dirigidos por los Black Belts.
- Las empresas exitosas en el uso y manejo de Lean y Six Sigma son aquellas que tienen la participación TOTAL de la alta gerencia.
- La mejora continua es una función estándar de las empresas de clase mundial, sea una fábrica de aviones, de carros o un puerto.
Vendrán los reportes de los participantes a sus jefes y empresas, y luego la implementación de todo lo visto y aprendido. Por tercera vez Lean Camp ha cumplido.
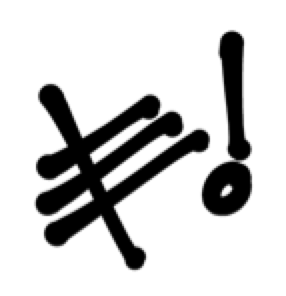
