Segunda Parte (¿Cuál sistema es más productivo el de empujar o el de halar las órdenes de proceso?)
Frecuentemente se escuchan opiniones a favor de uno u otro sistema para administrar las órdenes de trabajo. En el sistema de empujar, las órdenes se crean conforme un sistema de cómputo detecta que, con la cantidad de inventario que se tiene más lo que se está procesando, no alcanza para abastecer la demanda actual. En el sistema de halar, las órdenes se procesan tan pronto como aparece una señal (también conocido como Kanban) de que se debe producir una orden, usualmente por indicación de un cliente. Así descritos suenan muy parecidos, la diferencia está en que el sistema de empujar empuja las órdenes a la siguiente operación sin consideración de la capacidad instalada y en la segunda solo se hace si hay capacidad disponible. En ambos casos se puede tener una cantidad de órdenes sin comenzar acumuladas (Backlog), dependiendo de si se tiene balanceada la línea o no con el tiempo Takt.
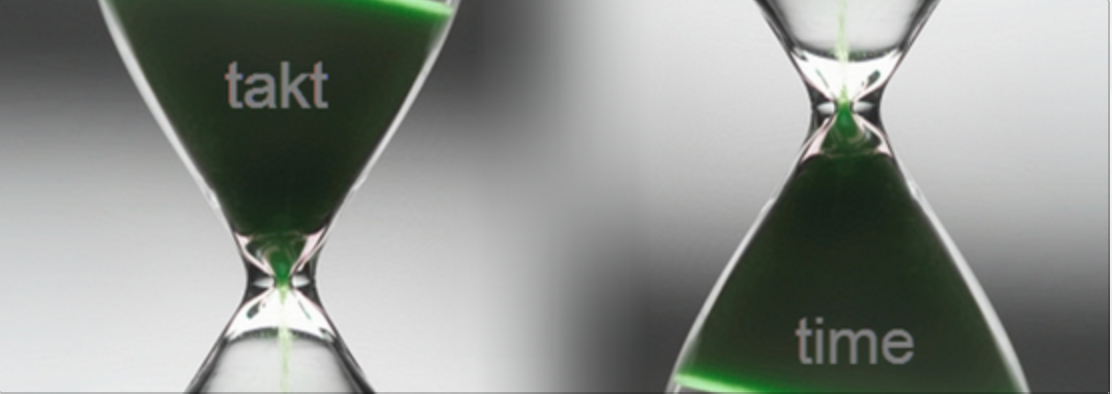
Veamos un ejemplo práctico. Supongamos que se tiene un proceso que consta de 3 operaciones Preparación, Transformación y Acabado, con tiempos de operación de un día y medio, medio día y dos días respectivamente, sin almacenamientos intermedios entre ellos. Asumamos que solo se tiene una estación para cada una de las tres operaciones, para efectos de simplificar el ejercicio. Además vamos a considerar que no hay variación en los tiempos de ciclo de cada operación, o que estamos operando con el promedio observado de una muestra representativa del proceso. En otra ocasión podemos hablar de casos más generales como una variación en los tiempos de procesamiento en cada operación y más generalmente cuando el cuello de botella se mueve en la línea, de una operación a otra, según la carga y mezcla de unidades que se procese.
Claramente solo podemos procesar tantas unidades como el cuello de botella lo permita. En este caso es la tercera operación que dura 2 días. Esto quiere decir que solo podemos procesar 3 unidades por semana, operando seis días y parando el sétimo para actividades de mantenimiento (fumigación de plagas, reparaciones de equipo, limpiezas profundas, etc.). Ésta es la capacidad instalada del proceso.
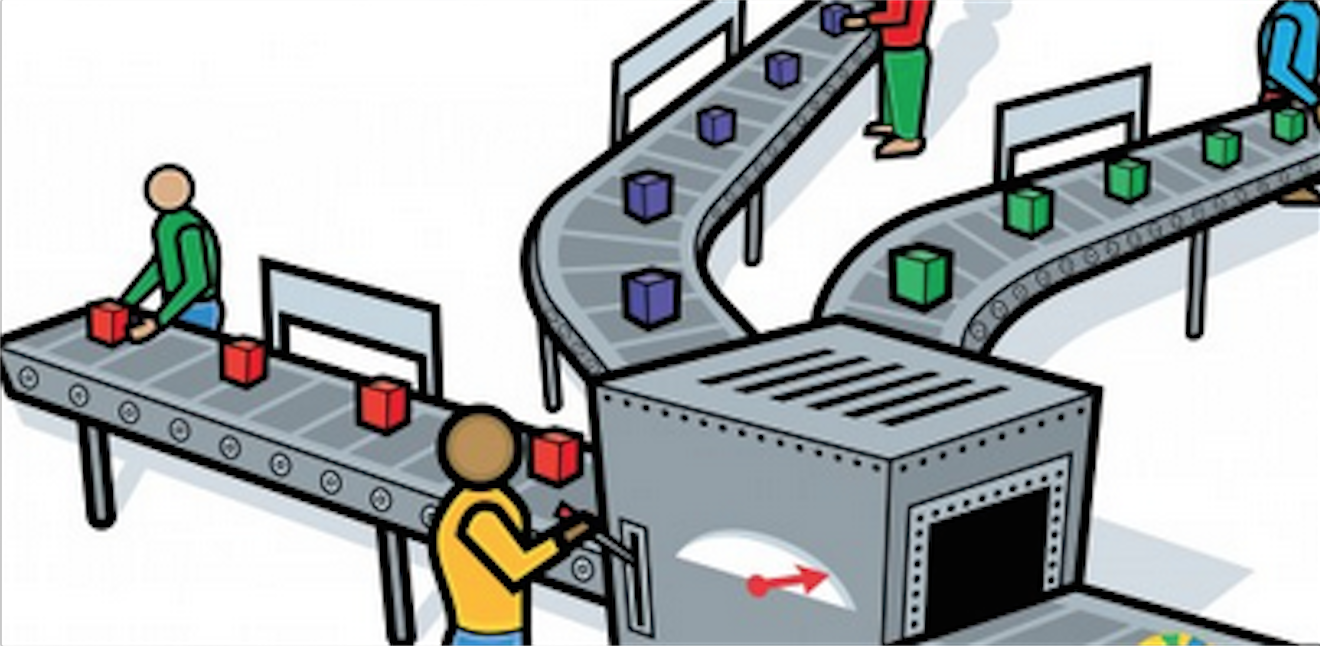
Bajo este escenario asumamos que nos ingresa una orden por semana. El primer día (digamos el lunes) se lo dedicamos a la primera operación de Preparación, la cual terminaría el martes al final de la mañana (consumiendo un día y medio de trabajo). El día martes en la tarde se hace la Transformación y el miércoles y el jueves se realizaría el Acabado, el viernes y el sábado no se operaría el proceso. Hemos completado la unidad y terminamos por la semana. El máximo nivel de inventario (WIP) durante esa semana es de una unidad y el tiempo de ciclo es de 4 días (una orden que se inicia el lunes se termina el jueves). El nivel de procesamiento por semana es en este caso de una unidad (el throughput es igual a uno).
Si la demanda sube a 2 unidades cualquiera de los dos sistemas ya sea de empujar o de halar indicaría a nuestro proceso que hay más demanda. El sistema de empujar posiblemente libere dos órdenes el lunes una de las cuales se terminaría el jueves (como en el caso anterior) y la otra el sábado (dos días después). El sistema de halar habría iniciado una el lunes y otra el miércoles. Ambos sistemas habrían conseguido un aumento en la productividad del 100%. Dos unidades procesadas en una semana (Throughput=2), el WIP habría subido a 1.33 unidades en promedio y el tiempo de ciclo total para las partes sería de 4 días.
Si aumentamos la demanda a tres unidades por semana, el sistema de empujar liberaría tres órdenes el lunes y el sistema de halar liberaría una el lunes, otra el miércoles y otra el viernes todas las semanas. Después de un par de semanas ambos sistemas estarían terminando las órdenes los martes, los jueves y los sábados, dando por resultado que se maximizaría la capacidad de procesamiento con tres unidades por semana (Throughput=3). El WIP sería de 2 (y no tres, ya que cuando la tercera unidad entra al sistema cuando la primera ha salido) y el tiempo de ciclo total de las piezas de 4 días.
A partir de aquí comienza la diferencia. Los que utilizan el sistema de empujar extrapolan que cuanto mayor sea el inventario en proceso (WIP) mayor será la cantidad de unidades procesadas, sin caer en la cuenta que esto solo sucede si el cuello de botella está subutilizado. Los que utilizan el sistema de halar se darían cuenta que no se puede aumentar el inventario en proceso, ya que este sería el que marca el paso.
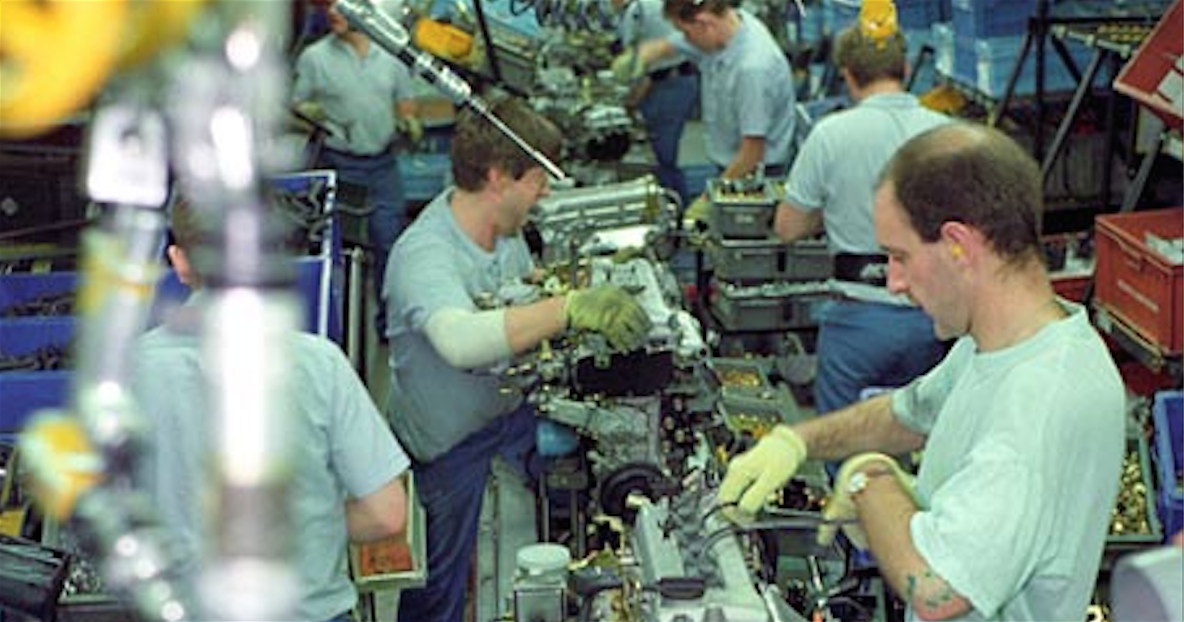
En conclusión, ¿cuál sistema es más productivo?
Ninguno per se. La productividad no depende del sistema que se utilice para liberar las órdenes. Depende del nivel de utilización y la eficiencia que se le dé al cuello de botella del proceso.
En cuanto a la cantidad de órdenes que manejamos en el sistema (WIP + Backlog) continuará creciendo en ambos sistemas si no se atiende oportunamente los aumentos de capacidad para balancearlos con la demanda (tiempo takt).
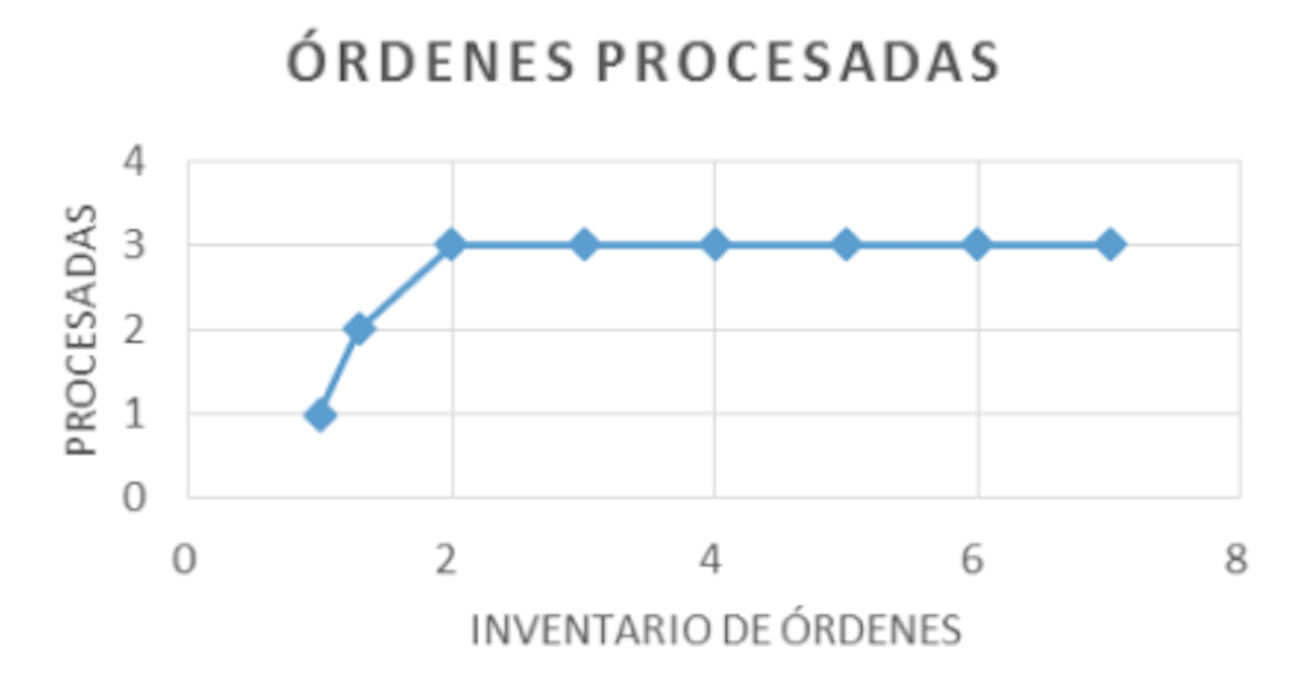
Arriba se muestra la relación entre el inventario en proceso y la cantidad de órdenes que se procesan en nuestro sistema y la relación entre el nivel del inventario y el tiempo de ciclo total.
Rolando Guido
Socio PXS